To produce crystalline zinc phosphate coating good for drawing coating obtained as per class A of IS 3618 Used in seven tank process.
STEP ONE(DEGREASING) :-
If the items to be phosphated are having oily layer of grease on them, then degreasing should be done prior to any process.
(1a) Alkaline Degreasing : Dissolve Meproche 245 at a ratio of 5% in water. Heat upto 80-85°C and dip the parts for 5 to 10 minutes. If will remove, Industrial
soil age, oil, grease etc. If will provide dirt free parts.
(1b) Test & Replenishment : Take 10 ml of bath material and titrate against 0.1 N Sulphuric acid, using
phenolphthalein as indicator. The pink end point should be between 60-65 ml. If found less add more Meproche 245. Every 0.8 kg of Meproche 245 per
1000 liters of barh material gives rise in pointage (No. of ml of 0.1 N sulphuric
acid), hence maintain the pointage between 60 and 65.
(1c): Remove the oil and grease from the top of the bath by skimming, as and when generated.
(2a) Solution Degreasing : Trichloro Ethylene or 1 : 1 : 1 Trichloro Ethyane or Meproche Chlorosol should be used. If the parts are small than Ultrasonic Vibration will accelerate the degreasing tremendously. Meproche Chlorosol is not only very effective but also cheaper than Tricholoro ethylene and 1:1:1 Trichloro Ethane.
Dip time = 10 to 15 seconds; Temperature = RT.
(or 5 to 10 minutes for DIP type degreasing at room temperature or 5 to 20 minutes at 85° c for vapor degreasing
STEP TWO :-
Rinsing : Rinse the components in hot/cold running water
STEP THREE :-
III(a) Pickling : Acid pickling bath should contain 14 to 18% concentration of Hydrocloric acid
18% Conc. from April to September. Add l litres of Meprolene per 1000 kgs of the bath material. This addition has to be done only once in the lifetime of the bath.
The temperature should be maintained at 25°C If the concentration goes down, temperature should be increased upto 28 to 30°C. When strength is 9% the temerature should be 35°C. Below 25°C the pickling is inefficient and above 35°C, HCL. is driven out which is injurious to
health. After the strength falls below 7% the bath should be drained off. There is iron build up in the pickling bath. The maximum iron content allowed is 12%.
III (b) Test for acid and iron content of the bath : Take 10 ml sample of the bath and add 90 ml of water to make it 100 ml.Take 10 ml of this diluted material and titrate against 0.2375 N sodium carbonate using screen methyl orange as
indicator. The solution turns red to green at the end point. The number of
mililitres of 0.2375 N sodium carbonate used is the percentage of acid in the bosh.
To this titrated sample add 5ml of B.D.S. solution (Add 0.8 gms of Barium Diphenyl Sulphonate to 50 mls of conc. Sulphuric acid and then add 450 gms of saturated hydrogen phosphate. The BDS solution is ready) and 5 ml of
conc.HCl. The colour of solution will turn red. This is titrated against 0.25 N Potassium Dichromate. At the end point the colour will change to
purple. The no. of mls of Pot.Dichrmate used is the percentage of iron in the bosh.
Inhibition : Meprolene inhibitor should be added in the beginning of every new pickling bath.1 liter of inhibitor is enough for 1 T of acid.
STEP FOUR : -
Water Rinsing : It is normally done twice to ensure acid free material. The water in the second bath is kept flowing. Acid content Tests on the rinsing baths should be made as in pickling bath. Maximum acid percentage allowed in first bath is 1%.
STEP FIVE (Optional):-
Activation : For good initial attack the parts should be dipped in Meprophos Activator Solution, The percentage of this activator should be 0.5% when it goes below 0.3% add more activator.
STEP SIX :-
Preparation of Phosphating bath solution:
(1) Make a 4 to 5% V/V solution of Meprophos 2614Z for preparation of bath solution.It will give 28 to 30 Pointage (the Pointage is defined as number of milli-litres of 0.1 N NaOH required to neutralize ten millilitre of bath solution).
(2)Initial addition of Meprox-II -accelerator-(app.one lit. per 1000 lit. of Solution) should be added to the phosphating bath.
(3)Add 50 to 100 gms iron pieces in the bath and keep it for five to six
hours, for Ageing so that darker and uniform phosphate coating may be obtained on the articles.
(4)Heat the bath to 80-85°C and this temperature should be maintained through out the
phosphating process..
(5)Again add Meprox II -app.one litre per KL .Dip the parts for 5 to 15 minutes in the bath for phosphating -a heavier coating can be obtained by increasing the dip time..
Replenishment : For every one point rise required in the strength of Meprophosphating bath 1.2 lit. material should be added per 1000 liters.
Test Pointage : Take 10ml of bath sample and titrate against 0.1N Caustic Soda solution (4.005gm/lit) keeping phenophthlein as indicator. At pink end point, the number of mls of 0.1N NaOH is equal to Pointage of the bath.
(6)Accelerator Test : Accelerator is consumed in the process of phosphating and also its strength keep on reducing with time even without doing the phosphating work.therefore accelerator test should be conducted from time to time as per method given below:
Take 50 ml of bath solution and add 5ml of 50 % sulphuric acid. Titrate it with 0.1N Potassium Permanganate solution till pink colour is stable for 15
seconds. Number of mls of potassium permanganate used is equal to Accelerator Pointage. This is to be maintained between 1.5 to 2.5.Every 1/2 lit. addition of Meprox II per thousand litres bath gives rise to Acceletor Pointage by one.
Important : To obtain best results, small additions of Chemicals (Both Meprophos 2614 Z and Meprophos Accelerator I) should be added every now and then in order to maintain the strength parameters. The principle is "Too small but too often".
STEP SEVEN :-
PASSIVATION (if required)
VII(a) Hot Passivation : Make a passivation solution by adding 800ml of Meprophos passivator per 1000 lit of water Heat it to 70°C. Dip the Meprophosphated part in it for a few seconds and let it dry in hot air after taking out.
Test : Titrate 10ml of bath solution against 0.1 N NaOH. The Passivation Pointage should be 0.75 max and 0.5 min.
or VII (b) Cold Passivator- Meproche 105 : Make a 10% solution of Meproche 105 cold passivator.Dip the phosphated components in the bath for 10 to 15 minutes and take them out.
Test & Replenishment : Test the bath from time to time for pH value.
When the pH comes below 9 add more passivator. CLEAN the bath from time to time ,if the level falls add more Meproche 105 and water in the suggested proportion.
STEP EIGHT :-
Lubrication : Such passivated parts (and sometimes without passivation) are to be lubricated, prior or drawing or packing finished products.
(a) Oil Lubrication : Dip the phosphated parts in Meprophos Lub oil prior to packing.
(b) Soap Lubrication : Dip the phosphated items in 6 to 10% concentration of Meprophoslube 3 The lubricating bath has to be maintained at , at 75 to 80°C. Phosphated parts should be kept for about 30 minutes. in the soap lubricating
bath. This is normally done prior to drawing operation.
Test : For maintenance of conc. of soap lubricating bath following test is
prescribed. Take 20ml of Meprophoslube solution, in a taroil flask. Add 5 mls of 50% sulphuric acid and place in hot water bath for about 30 min. Measure the oil layer.
Volume of layer X 10 = percentage of Meprophoslube 3.
Meprophos 40 : Cold zinc phosphate coating by dip process prior to painting Gives class B type of coating as per IS 3618.
Meprophos 60 M : Crystalline manganese phosphate corrosion resistant coating gives black coating after initial iron build up Good for bearing surface and oil retention.
Meprophos 301 : Zinc and manganese phosphate coating - To pickle phosphatise and passivate at room temperature (Three in one process)
Meprophos Activator 63 : Titanium based activator for closed grains use for phosphating. It is used to improve grain structure.
Meproche Passivator BA : Fixes the phosphate coat. Working temperature at 70 degree C. The jobs have to be dried by hot air after passivation.
Meproche activator 56 : Calcium based activator for close grains of Zinc Phosphate coating. Gives greyish coating.
Passivator 155 : Room temperature passivator. Dos not require hot air drying - Very efficient rust preventive.
DEGREASERS :
(I) Meproche 245 : Hot alkaline Degreases. For removal of oil, grease and light rust marks. Working temperature 70 degree C to 80 degree C.
Scope & Application :-
Meproche 245 is an alkaline degreaser formulated to remove oil, grease, heavy soils and dirt from the surfaces of ferrous
components. It is used prior to phosphating, electroplating, lacquering enameling , etc. The process is carried out by immersion at elevated temperature. (80 -90°C).
Description & Make-up Parameters:-
i) Apperarance : Off white powder.
Chemical Composition : Blend of surface active agents.
Solubility : Readily soluble in water
pH of working conc. : 12 - 13
ii) Concentration to be used : 5 - 10%
Working Temperature : 80 - 90°C.
Time of immersion : 5 - 15 min. (varies as per the oil/grease contaminants.)
Testing Control & Replenishment
10ml of bath solution is titrated with 0.1N H²SO using phenolphthalein as indicator. The end point is the change of pink colour to colourless.The volume of 0.1N H²SO consumed denotes the pointage. The pointage for 5% solution (W/v),
should be 60-65.
0.8 kg of Meproche 245 is required to increase the pointage by one for 1000 liters of bath volume.
Oil Content
During the process of cleaning, the oil gets removed from the components and floats on the surface of the bath. During the process, the separated oil is dispersed in the solution. This oil should be skimmed off periodically while the bath is not in
use. Depending upon the oil contamination the bath is discarded partially or fully for fresh make up.
Tank Material Construction
Mild steel tank is suitable for Meproche 245 bath.Safety & Handling Precaution :- Chemical contact with skin ,
eyes, mouth and clothings should be avoided. If it comes in contact with skin, eyes, flush off with water and pet medical attention. Use of gloves, boots,
eye shield are recommended while using Meproche 245.
Disposal :- Dilute & neutralise with acidic material before discarding.
(II) Meproche Degreaser 108 : Water based decreaser to remove light oil /
grease. Meproche Degreaser 108 is a specially designed produce to remove oil, dirt, grease, etc. which clung to the components because of engineering processes like, broaching, lapping, milling, drilling turning, grinding etc.
Method of use
Dilute the Meproche 108 by 10 to 12 times of water. Alternatively ultrasonic vibrations should be employed then efficiency is improved and time taken for process shall be app. 20 to 30 seconds, only. If oil content is more the solution may turn slightly milky. It can be sprayed by nozzles on the components in a closed compartment. It is very low foam type product.
Characteristics
Consistency |
Water white liquid. |
PH of 10% solution in distilled water |
8 max. |
Specific gravity |
app. 1.05. |
Flash Point |
Non - Inflammable |
(III) Meproche Chlorosul : Liquid degreaser - Non inflammable type - generally used in ultrasonic bath - removes oil & grease
instantly. Chlorosul is a specially designed mixture of chlorinated solvents to enable action of degreasing on steel and metal
components. The components can be degreased either by dip method or by ultrasonic
systems. The ultrasonic systems are very efficient and less time consuming.
Specifications
Appearance |
Water white liquid |
Specific Gravity |
1.4/1.45 |
Flash point |
Does not flash. |
Hints for uses
1) Materials/components can be degreased by dip method, in which the dip time ranges from 8 to 10 minutes.
2) Materials can be degreased by ultrasonic method in which method the time of dip is
few seconds .However this method
is far more efficient.
3) After some time the oil and grease so stripped shall float over the surface which
should be skimmed out.
4) The components can be vapour degreased to reach at the intricate crevices.
(IV) Meprox I Accelerator : Used along with Merophos 2614 Z to accelerate the phosphating process and remove the gases formed.
(V) Merpoche Derust 88 : Inhibited phosphoric acid based - for removal of light rust marks from surface. Used prior to phosphating for better surface activity. Parts should be rinsed after derusting.
(VI) Meprophos 'H' : Hydrochloric Aid Inhibitor - to be used during acid pickling - to be put only once in the acid bath.
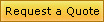 |